CDMO
Contract Development and Manufacturing Organization
北极星药业(瓦卡维尔)Polaris Pharmaceuticals - Vacaville
我们拥有完备且先进的生物制药生产设施,内部执行从细胞库生产到填充和完成的所有制造过程。在质量控制和质量保证方面,我们具备广泛的内部能力,以确保药品生产过程中的合规性、一致性、质量和安全性。
Polaris团队在基于大肠杆菌的表达和纯化系统方面拥有丰富经验,可实现重组蛋白的高水平表达。小规模的开发和优化工作在摇瓶和5L工艺开发发酵罐中进行,而GMP生产则在200L发酵罐中进行。
我们设计并实施与开发阶段相匹配的客户特定流程,并考虑到商业可行性和产品生命周期。开发和临床前活动作为非GMP研究进行,而早期的临床生产则由合格的方法和工艺支持,遵循cGMP准则和惯例。
通过灵活的方法和阶段适用的活动,我们在早期阶段实现了成本节省,同时提供了必要的全面监管支持,为成功推进项目进入后期阶段和商业化cGMP生产奠定了基础。
Process Development
We offer a full suite of development services for biologics derived in microbial hosts using small scale fermentors, centrifuges, microfluidizers and chromatography systems.
- Upstream process optimization up to 5L scale
- Downstream process optimization
- Process scalability testing
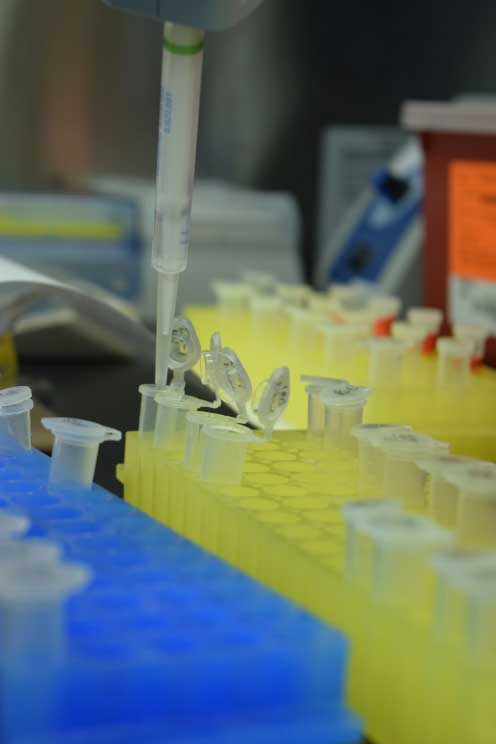
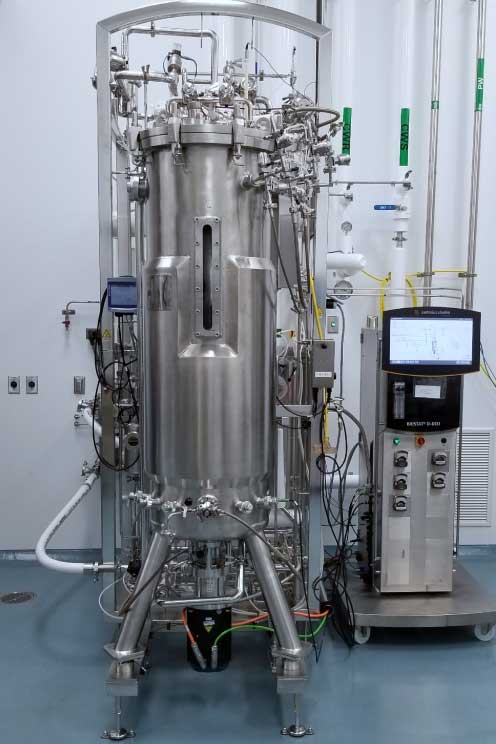
Fermentation
Our team has expertise in all microbial processes including cell bank generation, fermentation, harvest, and cell lysis. They are especially accomplished in the area of proficiency in inclusion body refolding.
-
- Separate Area for Upstream Manufacturing
- 200L Stainless Steel (Working Volume) Fermentor
- Alfa Laval Centrifuge
- Microfluidics 7125-20K Microfluidizer
- 5 x 200L Harvest and Holding vessels
- 20L to 500L Single Use Buffer Preparation Tanks
- Buffer and Media prep
Purification
Our team has expertise in chromatography and UF/DF. We are especially accomplished in manufacturing pegylated proteins.
- Separate Downstream Manufacturing Area
- 3 Chromatography Skids
- Tangential Flow Filtration (TFF) Systems
- Dedicated Column Packing Area
- 20L – 2000L Single Use Buffer Preparation Tanks
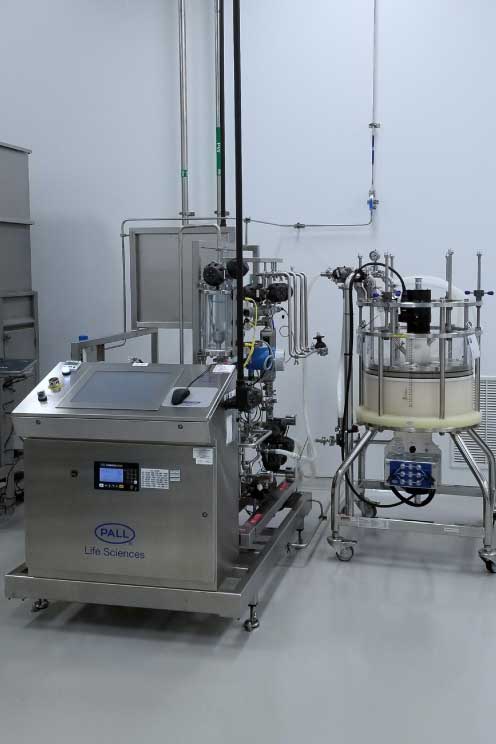
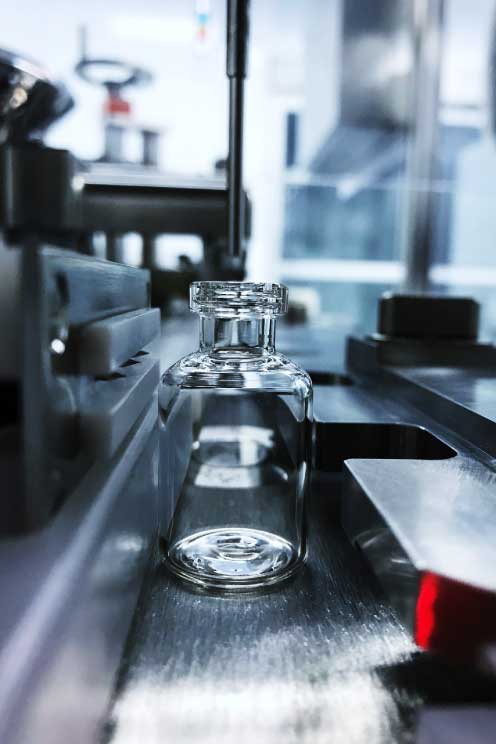
Fill Finish
We offer exceptional fill-finish operations and can provide all necessary elements needed to deliver high-quality parental products for clinical needs.
- Fill-Finish operation in an ISO 5 Environment
- cGMP compliant Fill-Finish Suite
- Bosch FLT Filling Machine in an Active RABS Enclosure
- In-house Visual Inspection and Labeling
- Up to 10,000 vials per batch filling capacity
Quality Assurance
We produce drug products following Current Good Manufacturing Practices. We have an experienced Quality Assurance Team that is committed to complying with all appropriate regulations. Our team is efficient and experienced in the release of drug product components, intermediates, and final products.
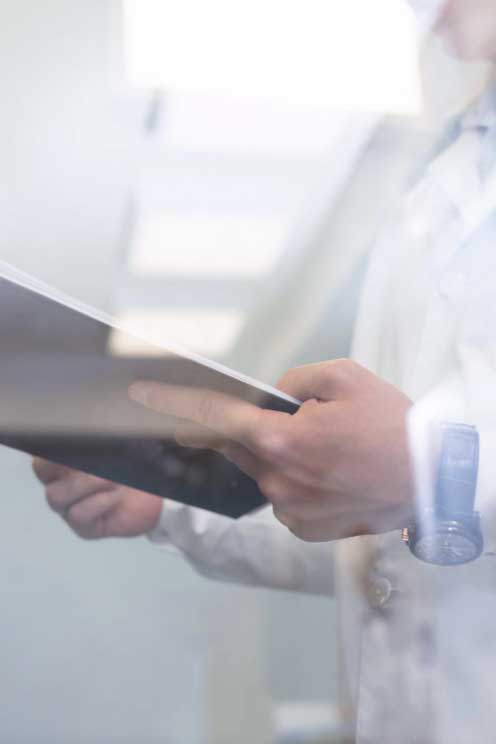
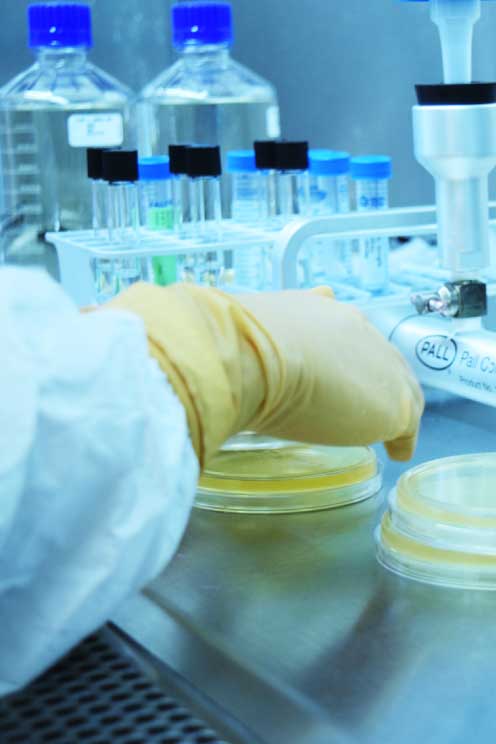
Quality Control
We have a comprehensive QC team with the ability to perform most Quality Control testing on site.
- Analytical method development capabilities
- 5 High Performance Liquid Chromatography Machines
- Process intermediate microbial property testing abilities.
- Ability to test microbiological properties of process intermediates
- Ability to perform stability testing
- Ability to perform testing for product strength, potency, identity, purity, and safety
- Ability to effectively monitor the quality of manufacturing areas and utility systems
- Ability to test microbiological properties of process intermediates
- Stability storage at multiple temperatures and time points
- Continuous chamber monitoring and emergency power system
Facility
Our state-of-the-art facility is 7,500 ft2 of manufacturing space with a 28,000 ft2 total footprint. Our facility consists of two manufacturing trains, 2 QC labs, 2 PD labs, a warehouse, offices, and utility rooms. Our clean and plant utilities are validated and routinely tested supporting manufacturing and laboratory areas.
- Purified Water (PW) and Water for Injection (WFI) Generation
- Clean Dry Air Generation
- In-House Oxygen Generation
- In-House Nitrogen Generation
- Automated Clean-In-Place Skids
- Cooling water and Plant Steam Generation
- Emergency electrical Generator
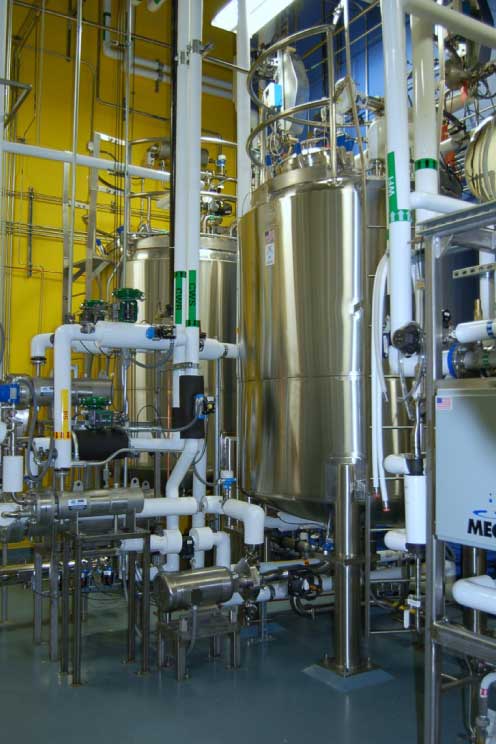
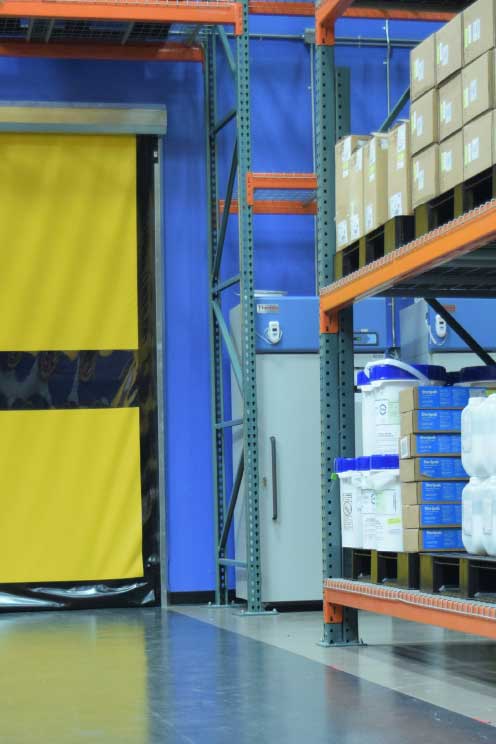
Warehouse
All final product and raw materials are stored in our temperature-controlled and access-controlled warehouse. Inventory is tracked in our electronic inventory tracking system for proper traceability and accountability. Final product storage is validated and backed up by our emergency backup system.