CDMO
Contract Development and Manufacturing Organization Vacaville California
Complete state of the art biopharmaceutical manufacturing facility. We perform all manufacturing processes in-house from cell bank production through fill and finish. We have broad in-house capabilities in Quality Control and Quality Assurance to ensure compliance, consistency, quality, and safety during the manufacturing of drug product.
The Polaris team has extensive experience in generating E. coli-based expression and purification systems for high level expression of recombinant proteins. Small-scale development and optimization is performed in shake flasks and 5L Process Development fermentors. GMP manufacturing is performed in a 200L fermentor.
We design and implement customer-specific processes matching the stage of development with commercial viability and product lifecycle in mind. Development and Preclinical activities are executed as non-GMP studies. Early Clinical Manufacturing is supported with qualified methods and processes following cGMP guidelines and practices.
Our flexible approach and utilization of stage appropriate activities results in cost savings for early stages while providing assurance of compliance of full regulatory support necessary to set up successful further advancement of programs into the late stage and commercial cGMP manufacturing.
Process Development
We offer a full suite of development services for biologics derived in microbial hosts using small scale fermentors, centrifuges, microfluidizers and chromatography systems.
- Upstream process optimization up to 5L scale
- Downstream process optimization
- Process scalability testing
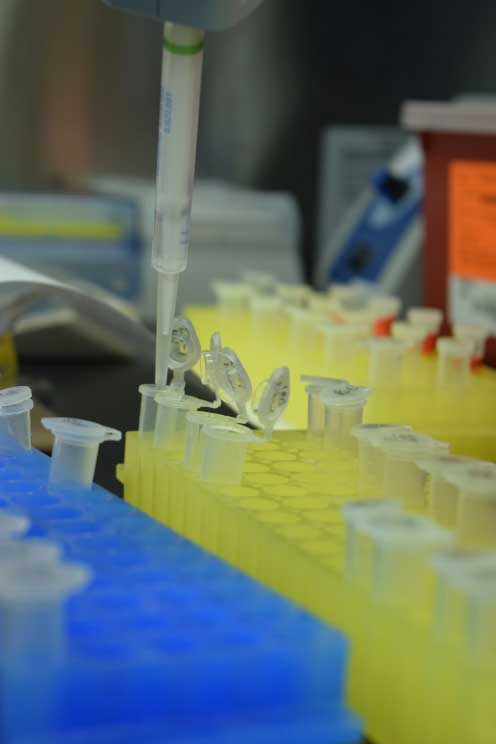
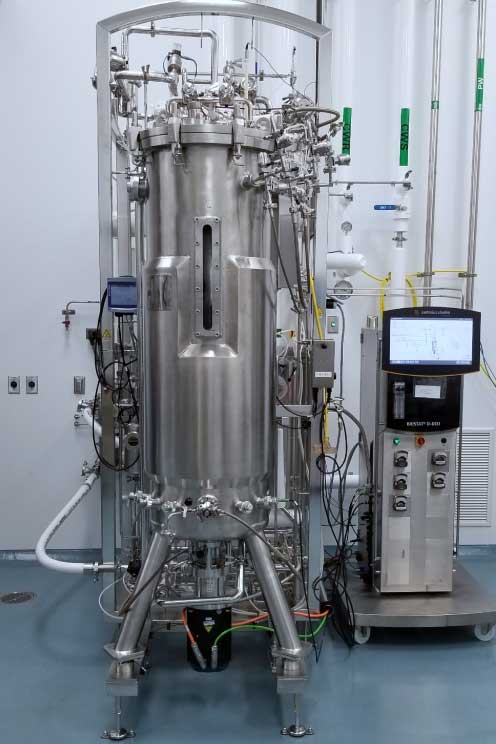
Fermentation
Our team has expertise in all microbial processes including cell bank generation, fermentation, harvest, and cell lysis. They are especially accomplished in the area of proficiency in inclusion body refolding.
-
- Separate Area for Upstream Manufacturing
- 200L Stainless Steel (Working Volume) Fermentor
- Alfa Laval Centrifuge
- Microfluidics 7125-20K Microfluidizer
- 5 x 200L Harvest and Holding vessels
- 20L to 500L Single Use Buffer Preparation Tanks
- Buffer and Media prep
Purification
Our team has expertise in chromatography and UF/DF. We are especially accomplished in manufacturing pegylated proteins.
- Separate Downstream Manufacturing Area
- 3 Chromatography Skids
- Tangential Flow Filtration (TFF) Systems
- Dedicated Column Packing Area
- 20L – 2000L Single Use Buffer Preparation Tanks
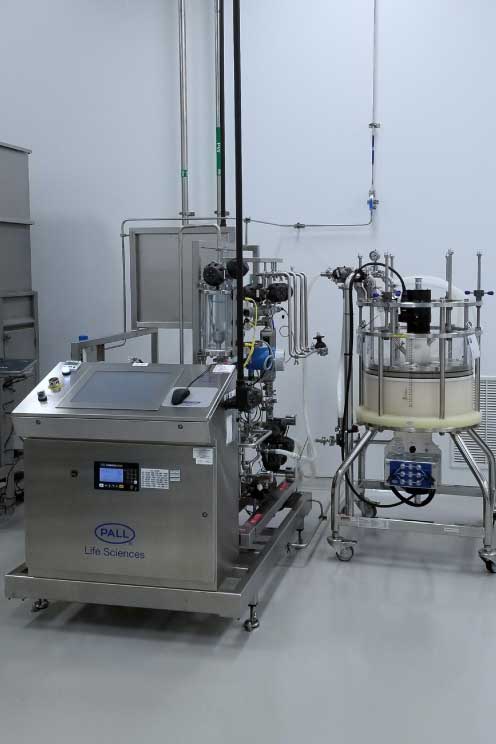
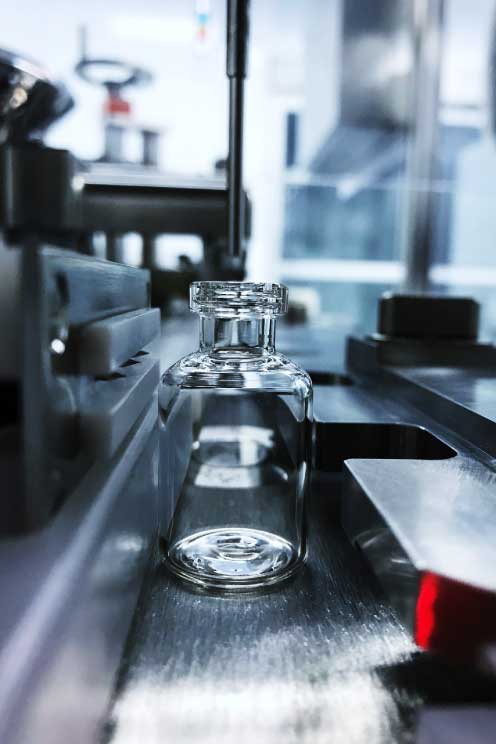
Fill Finish
We offer exceptional fill-finish operations and can provide all necessary elements needed to deliver high-quality parental products for clinical needs.
- Fill-Finish operation in an ISO 5 Environment
- cGMP compliant Fill-Finish Suite
- Bosch FLT Filling Machine in an Active RABS Enclosure
- In-house Visual Inspection and Labeling
- Up to 10,000 vials per batch filling capacity
Quality Assurance
We produce drug products following Current Good Manufacturing Practices. We have an experienced Quality Assurance Team that is committed to complying with all appropriate regulations. Our team is efficient and experienced in the release of drug product components, intermediates, and final products.
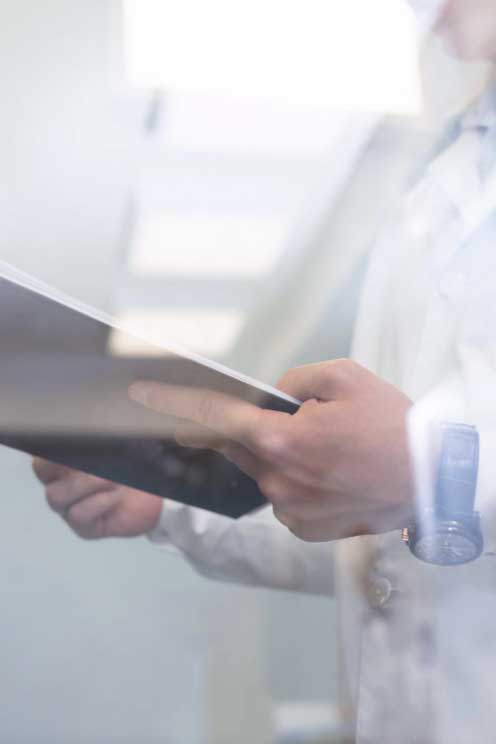
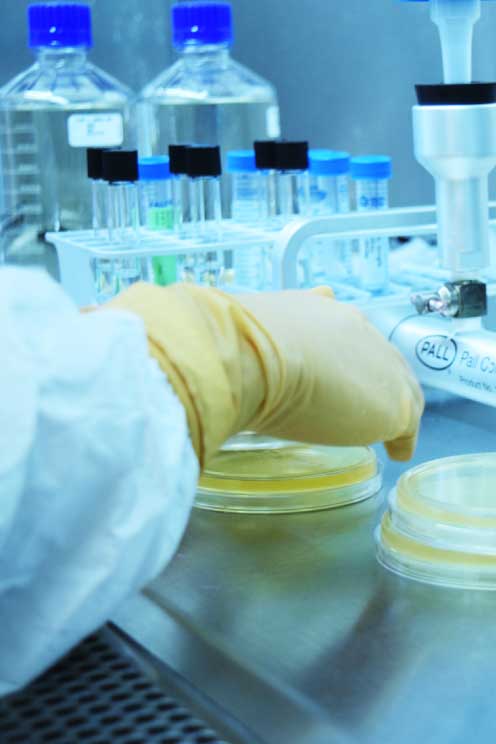
Quality Control
We have a comprehensive QC team with the ability to perform most Quality Control testing on site.
- Analytical method development capabilities
- 5 High Performance Liquid Chromatography Machines
- Process intermediate microbial property testing abilities.
- Ability to test microbiological properties of process intermediates
- Ability to perform stability testing
- Ability to perform testing for product strength, potency, identity, purity, and safety
- Ability to effectively monitor the quality of manufacturing areas and utility systems
- Ability to test microbiological properties of process intermediates
- Stability storage at multiple temperatures and time points
- Continuous chamber monitoring and emergency power system
Facility
Our state-of-the-art facility is 7,500 ft2 of manufacturing space with a 28,000 ft2 total footprint. Our facility consists of two manufacturing trains, 2 QC labs, 2 PD labs, a warehouse, offices, and utility rooms. Our clean and plant utilities are validated and routinely tested supporting manufacturing and laboratory areas.
- Purified Water (PW) and Water for Injection (WFI) Generation
- Clean Dry Air Generation
- In-House Oxygen Generation
- In-House Nitrogen Generation
- Automated Clean-In-Place Skids
- Cooling water and Plant Steam Generation
- Emergency electrical Generator
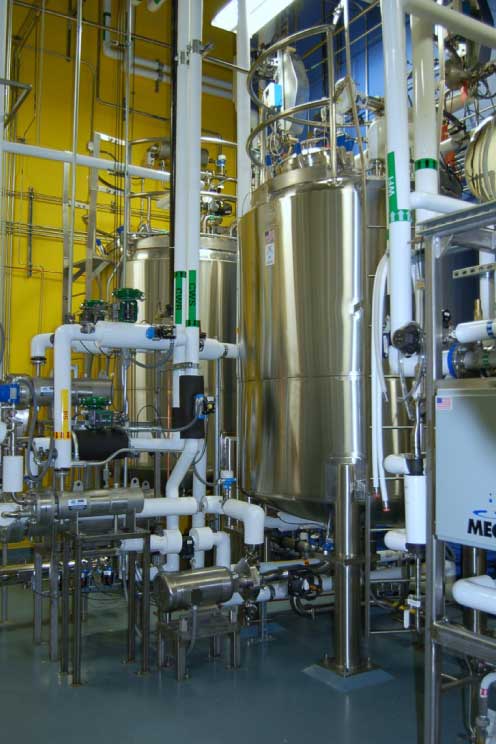
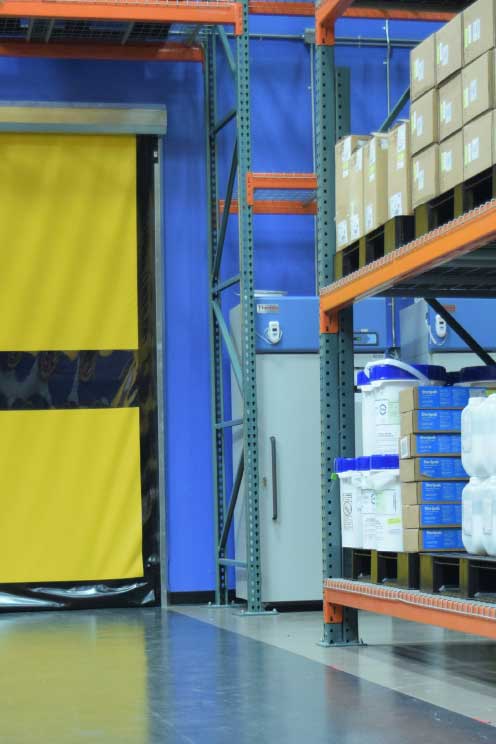
Warehouse
All final product and raw materials are stored in our temperature-controlled and access-controlled warehouse. Inventory is tracked in our electronic inventory tracking system for proper traceability and accountability. Final product storage is validated and backed up by our emergency backup system.